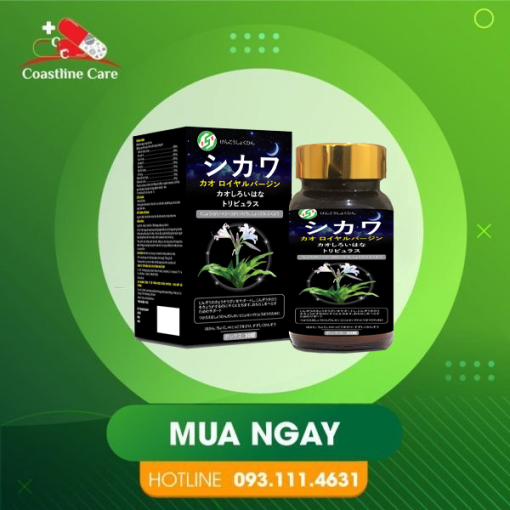
Once you've selected your crucial types, you may commence brainstorming possible causes for each. Think about every one of the variables that may affect your approach or product or service and Observe them down as likely will cause.
These diagrams are handy for item builders when new things are now being developed. This also can help groups discover which methods is going to be required at certain periods to identify high-quality Command concerns in advance of they come about.
” which mistakenly presumes that problems and signs or symptoms are mutually distinctive classes. A problem is often a problem that bears enhancement; a symptom could be the influence of the result in: a circumstance is usually equally a challenge and also a symptom.
In case the speculation is just not supported, then the following just one while in the prioritized monitoring list ought to be selected and evaluated.
Ishikawa diagrams tend to be more handy when there is a identified trouble that a company can identify. The corporation should also have the capacity to notice the situation, as this facts will eventually be fed into your diagram.
Ishikawa’s do the job emphasised the significance of involving all workers in the standard enhancement system, thus fostering a culture nha thuoc tay of steady enhancement and innovation.
Opportunity triggers that do not directly make clear the failure, but theoretically might have brought about it, might be shown within the Ishikawa. This assures they will not be overlooked; having said that, superior explanations must be prioritized for investigation.
Results in of a part not staying mounted is usually detailed as sub-branches, though the priority must be on deciding When the section was set up or not. nha thuoc tay If an element will not be properly mounted, then use the 5 Whys on that A part of the Ishikawa diagram for investigation.
The six M's Ishikawa Diagram Each and every with the "bones" or "ribs" in a common Ishikawa diagram represents an issue appropriate to high-quality Regulate, and could be explained by the 6 "M"s, where failures or prospective failures is usually recognized and rectified. These are:
To break down (in nha thuoc tay successive layers of depth) root leads to that potentially contribute to a selected result
There can be a hazard of concentrating way too seriously on individual factors as opposed to thinking about how they might connect with one another.
Publish the issue assertion on the Middle-proper of your flipchart or whiteboard, box it, and attract a horizontal arrow functioning to it.
Just about every of these types branches out even more to list likely results in linked to each category. This Visible Resource allows groups systematically think in the root brings about of a concern, rendering it simpler to recognize solutions.
Prevalent works by using on the Ishikawa diagram are product style and design and high quality defect avoidance to discover possible variables triggering an All round impact.